The EPRI Electrostatic Precipitator
Compliance Assurance Monitoring Protocol Project
|
Richard D. McRanie
RMB Consulting & Research, Inc.
INTRODUCTION
As everyone is aware by now, the Environmental Protection
Agency (EPA) has promulgated the Compliance Assurance Monitoring (CAM)
rule. This rule will affect virtually all electric utility generating plants.
The primary impact will be to require that utilities address the particulate
mass emission compliance status of their particulate control devices on
a frequent basis. The mechanism for accomplishing this may be very different
from plant to plant and may be difficult to develop.
There is significant potential that an electrostatic precipitator
(ESP) performance model will provide a useful mechanism for evaluating
the performance of ESPs under the CAM rule. These models predict the performance
of ESPs from fundamental principals and have proven to be accurate when
calibrated (set up) with actual operating data. The Electric Power Research
Institute (EPRI), in cooperation with several individual electric utilities,
has initiated an Tailored Collaboration (TC) project to investigate the
use of ESP models under CAM. RMB has been in contact with EPA throughout
the rulemaking process and EPA has agreed to allow the utility industry
to develop its own ESP CAM protocol for inclusion in the CAM Guidance Document.
Assuming this project is successful, a "standard" CAM protocol
for ESPs will save the electric utility industry a significant amount of
effort and money in negotiating with the various regulatory agencies and
demonstrating case-by-case protocols. The remainder of this paper is a
discussion of the CAM rule, its impact on the electric utility industry
and a description of the EPRI CAM project.
OVERVIEW OF THE CAM RULE
The CAM rule was promulgated by EPA on October 22, 1997.
It is the offspring of the fundamentally flawed proposed Enhanced Monitoring
(EM) rule which suggested an absolute demonstration of compliance with
any applicable emission standard. The proposed EM rule was so burdensome,
and impacted so many industries and very small sources that it soon became
obvious to EPA that the rule would not survive the political and technical
attacks. Consequently, the EM rule was dropped and development of the CAM
rule was reassigned from the EPA Enforcement Division to the Office of
Air Quality Planning and Standards.
The clear difference between the EM rule and the CAM
rule is that the CAM rule only requires a "reasonable assurance of
compliance" rather than the "absolute measure of compliance"
contemplated by the proposed EM rule. In addition, it has a reduced impact
for most industrial sources. In the electric utility industry, virtually
all coal-fired units will be impacted relative to particulate emissions
and the related particulate control devices.
The CAM rule is very simple in concept but far-reaching
in application. The premise of the CAM rule is that, if a control device
is properly operated and maintained and has defined operational criteria
and compliance criteria, then emissions will be reduced. A quote from a
speech by a closely associated EPA person sums up the rule well, "Our
objective is to make sure that the control device operator pay as much
attention to the control device as he does to the production process. We
want him to be ready for a compliance test every day."
We also have to mention the Credible Evidence (CE) rule
that was independently promulgated by EPA. The essence of the CE rule reads
as follows:
"For the purpose of submitting compliance certifications
or establishing whether or not a person has violated or is in violation
of any standard of this part, nothing in this part shall preclude the use,
including the exclusive use, of any credible evidence or
information, relevant to whether a source would have been in compliance
with applicable requirements if the appropriate performance or compliance
test or procedure had been performed."
This simple CE rule must be kept in mind as one works
through the requirements and implementation of the CAM rule.
In general, CAM impacts all sources that are subject to
the Title V permit program and are classified as "major sources"
for any applicable emission standard. Relative to our discussion today,
if the particulate emissions are greater than 100 tons/year uncontrolled,
and the boiler is equipped with a control device, then CAM applies. (Obviously,
boilers equipped with control devices for SO2 and NOX
are also impacted but that discussion is beyond the scope of this paper.)
Since virtually every coal-fired utility boiler meets the applicability
definition, a considerable population of ESPs and baghouses are impacted.
(Baghouse CAM approaches are also not discussed in this paper because they
should be fairly straightforward.)
Under the CAM rule a utility generating unit with an ESP
or baghouse must:
- Develop parameter monitoring for the control device,
- Establish indicators ranges,
- Respond to excursions,
- Take corrective action,
- Reports excursions in semiannual compliance reports as
"possible exceptions to compliance."
In addition, the CAM rule requires any affected unit to
have a CAM Protocol in the Title V permit that contains:
- A description of the monitoring,
- Parameter values or procedures that define excursions,
- QA/QC procedures and schedules,
- Technical justification that the monitoring will ensure
"reasonable assurance of compliance."
The fundamental question then becomes, how do we develop
a CAM Protocol for ESPs?
POSSIBLE CAM PROTOCOL APPROACHES FOR ESPs
A number of possible CAM Protocol approaches come to mind when relating
particulate mass emissions to a "reasonable assurance of compliance."
Included are:
Direct particulate mass emissions monitoring would obviously
be the choice if the technology was available. Unfortunately, we do not
believe this technology is ready for compliance determination purposes.
A number of different particulate mass monitors have recently been tested
by EPA as a part of the hazardous waste incinerator rulemaking. EPA used
a new Performance Specification (PS-11) to evaluate the performance of
particulate mass monitors. Figure 1 shows the performance of one of the
EPA tested monitors. Obviously, the middle line through the data represent
the linear best fit of all the data. The next set of boundary lines represents
the 95% confidence interval. One must be careful to recognize that the
confidence interval tells us nothing about any individual data point. The
confidence interval lines only say that, if the identical series of tests
was repeated, there is a 95% percent probability that the second data set's
linear best fit line would lie between the confidence interval lines.
More important to compliance determination issues is the outermost set
of boundary lines, which are the 75% tolerance intervals. What these lines
tell us is that, if we take more individual data points, there is a 95%
probability that 75% of the data points will lie somewhere within these
lines. For example, if we look at a monitor response of 30 on Figure 1,
75% of the data points will lie between approximately 18 and 65 mg/dscm
particulate mass. Clearly, this level of particulate monitor performance
is not satisfactory for compliance determinations.
Since these tests were performed on incinerators with extremely low mass
emissions, the monitor vendors and EPA are of the strong opinion that much
of the "error" is due to the particulate test method (EPA Reference
Method 5). It is obvious that particulate test methods perform poorly and
have high variability at low particulate concentrations. We are, therefore,
incorporating particulate monitor tests into the EPRI CAM project. It is
significant to note that, if a utility were to decide to use a particulate
monitor for CAM compliance purposes, there would be no way to compensate
for any test variability that might be experienced.
The test and cap approach is very simple and straightforward
and was the original particulate approach contemplated by the EM rule.
This approach is to simply perform a compliance test and, if the control
device (ESP or baghouse) showed in compliance operation, then future operation
would be limited to the opacity during the compliance test plus 2%. In
other words, if compliance was demonstrated at 5% opacity, future operation
would be capped at 7% opacity. While this approach may be applicable to
some baghouses, it would seriously compromise the ability of an ESP to
use performance margin that had been purchased by the utility.
Opacity/mass correlation and ESP power/mass correlation
are other "compliance demonstration" techniques that have been
used by utilities and states in the past. Given a consistent supply of
coal and some ESP performance margin, opacity/mass correlation might be
a useful approach under certain circumstances. ESP power/mass correlation
does not appear to be a useful approach because the particulate collection
rate in an ESP depends on the specific section of the ESP where the power
is applied. The permeations and combinations are just too complex for a
simple correlation to handle adequately.
It is believed that the ESP model extrapolation has a
high probability of being a useful CAM tool for ESPs. Both EPA and EPRI
have developed ESP performance computer models over the past 15 years that
calculate ESP performance on fundamental principles. It has been shown
many times that, when calibrated to a specific ESP, the models perform
very well in predicting ESP performance changes from physical or electrical
modifications to the ESP. The ESP model also has the capability of accounting
for power variations in the various ESP electrical sections and for sections
that are out of service. The model inherently compensates for fuel changes
that influence the ash resistivity because these changes are reflected
in the voltage and current relationships. In addition, using an ESP model
for CAM will allow the utilization of ESP performance margin while other
approaches are likely to restrict the use of margin. On the other hand,
ESPs without margin will experience problems under any conceivable CAM
implementation scenario, including use of a model.
Another advantage of using the model is that it can be
used for planning purposes. For example, one could examine the potential
impact of a fuel change or evaluate the effect of additional ESP electrical
sections being shorted.
What has not been fully demonstrated is the reliability
of the models over a wide range of ESP operational characteristics. This
is the primary objective of the EPRI project. If the models are shown to
have adequate "prediction range" then they will be extremely
useful in the CAM rule context. The major disadvantage is that the model
may be relatively expensive to set up and calibrate.
It is important to understand that, even under the best
of circumstances, an ESP model will not provide information sufficient
for absolute compliance determination purposes. It is believed, however;
that the information will be more than adequate for CAM where the criteria
is "a reasonable assurance of compliance."
THE EPRI ESP CAM PROTOCOL PROJECT
The EPRI CAM project has been in place for over a year.
The objectives of this project are to: (1) develop a demonstration test
plan suitable for thorough evaluation of the ESP model capabilities; (2)
conduct field demonstration tests over a range of ESP operating conditions;
(3) analyze the field data with 3-4 different ESP models to evaluate the
range of the models, and; (4) determine the minimum number of calibration
runs required to obtain meaningful results for CAM purposes (i.e., to have
a reasonable assurance of compliance).
The primary activities to date have been to follow EPA
rule making activities, to develop various implementation scenarios and
to prepare a draft CAM protocol for ESPs. After the rule was finalized,
planning was begun for field demonstration of the ESP CAM protocol.
The first activity was to select a site for the field
tests to demonstrate the protocol. The primary criteria for the first test
site included:
- A large ESP with considerable performance margin was
deemed essential so that the range of the model could be demonstrated.
- A base loaded generating unit that could be operated
at or near full load for extended periods.
- A willing host utility.
After evaluating several candidate units among the project
supporters, Georgia Power Company's Yates Unit 7 was chosen. The unit is
nominally rated at 350Mw and is equipped with an ESP that has considerable
margin and sectionalization. The allowable particulate mass emission rate
is 0.24 lb/mmBtu and the normal emission rate is approximately 0.015 lb/mmBtu.
This range allows considerable flexibility for testing purposes.
The tests are scheduled to begin the first week in June
and are anticipated to take two weeks. This is not to suggest that a model
calibration for any specific unit will take two weeks. The plan is to take
considerably more data than necessary during this demonstration period
so that the models can be fully exercised under a wide variety of conditions.
It has been shown over the past several years that the
available ESP models can be calibrated to a given coal, ESP and operating
condition. What is not known is the "range" of the models over
a variety of conditions. For example, given adequate emissions test, particle
sizing and ESP electrical data, a model can usually be calibrated to produce
a perfect fit to the test data. This is done by adjusting certain fitting
factors (primarily rapping reentrainment and sneakage) in the model. After
calibration, the model can be used to evaluate general operating condition
changes such as stack flow, inlet particulate loading, addition of plate
area, loss of electrical fields and changes in ESP power. The magnitude
of impact on ESP performance, either positive or negative, can be clearly
seen. What has never been documented in the public domain, however, is
the accuracy of these "off calibration" predictions. (Private
data show that the models do a very excellent job of predicting ESP performance
for plate area additions and field splits.)
To meet the project objectives, a series of field tests
will be performed. The test design will evaluate the two primary performance
reduction modes of an ESP - complete shorting of electrical sections and
reduced power in all sections caused by unfavorable fuel or flue gas conditions.
All tests will be run at nominal full load. A general demonstration test
protocol is shown below. This test protocol is much more elaborate than
one might expect for a final CAM calibration protocol because it is designed
to evaluate a broader range of conditions than would otherwise be necessary.
For example, it will likely not be necessary to perform particle sizing
tests to calibrate the model because coal-fired utility boilers produce
similar sized ash particles and a default particle size distribution is
usually satisfactory.
A. The unit will be stabilized at full load with normal
excess O2.
1. ESP inlet and outlet particle size distribution tests
will be performed.
2. ESP inlet and outlet particulate mass loading tests will be performed.
(Paired test trains will be used for all particulate mass tests so that
the precision of the test method can be determined.)
3. ESP power, opacity and boiler data will be collected.
4. The models will be exercised and calibrated to produce a fit with the
field data.
B. One or two ESP sections will be removed from service.
(Opacity will be used as a guide for how many sections to remove. A measurable
opacity increase will be needed.)
1. ESP outlet particle mass and size distribution tests
will be performed. (We can safely assume that the inlet conditions have
not significantly changed.)
2. ESP power, opacity and boiler data will be collected.
3. The models will be exercised and calibrated to produce a fit with the
field data.
C. The process described in B will be repeated until 3-4
different conditions have been tested.
D. The process described in A-C above will be repeated except that power
on all sections will be reduced (as opposed to taking out entire electrical
sections) to simulate unfavorable coal ash or flue gas conditions.
E. Three or four replicate test conditions will be done
to examine reproducibility of the ESP and boiler conditions.
Calibrated data sets for all of the data runs described
above will be produced using 3-4 different ESP models. By evaluating the
difference in the amount of "correction" needed to produce a
calibration across the test conditions, the ability of the models to track
the varied conditions will be determined. A model prediction error analysis
will be done to determine variance in the prediction. It is probable that
a multiple parameter relationship will be discovered. The various models
will also be evaluated for ease of use and accuracy of prediction.
A final report will be prepared for the participating utilities and a generic
"standard" CAM protocol will be submitted to EPA for inclusion
in the CAM Guidance Document.
CONCLUSIONS
The CAM rule and its impact on the electric utility industry
is a "fact of life" and the industry must implement the provisions
of the rule. It is believed that an ESP performance prediction model can
have a very important role in demonstrating a "reasonable assurance
of compliance" for particulate emissions as required by the CAM rule.
The EPRI CAM Protocol project is designed to evaluate the possibility of
using an ESP model for CAM and, if successful, prepare a "standard"
protocol for inclusion in EPA's CAM Guidance Document. If the project is
successful, costs of developing site specific ESP CAM Protocols will be
significantly reduced.
Figure 1
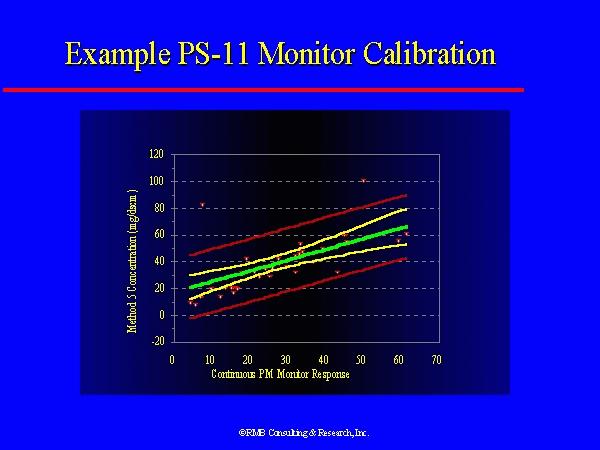
| Home | News
| Services | Contact
| Feedback |
Agora Environmental Consulting
Last Revised: February 25, 2008
|